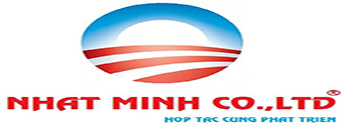
HƯỚNG DẪN CÁCH KHẮC PHỤC LỖI QUY TRÌNH HÀN SÓNG
Thoạt nhìn, máy hàn sóng và quá trình này dường như là rất đơn giản vì chỉ có bốn chức năng cơ bản. Vận chuyển PCB bằng băng tải với một tốc độ không đổi xuyên qua quá trình tẩm ướt flux, gia nhiệt hấp flux và hàn. Tuy nhiên, khi bạn kết hợp nhiệt độ, phản ứng hóa học, vật lý, vật liệu PCB linh kiện, cách thiết kế và bố trí PCB, bây giờ bạn có một quá trình rất phức tạp với nhiều biến tương tác với nhau. Hãy nhìn vào một số chức năng cơ bản của máy hàn sóng dưới đây để có thể hiểu và có cách thức làm thế nào đó với mỗi thành phần có thể ảnh hưởng đến quá trình quan trọng này.
BĂNG TẢI: (conveyor)
Chức năng hệ thống băng tải là để chuyển tải các PCB vào máy, chạy thông qua các quá trình và ra khỏi máy. Băng tải phải giữ chặt PCB trong khi chuyển PCB ở một tốc độ không đổi. Tốc độ băng tải kiểm soát các thông số quá trình như độ dốc gia nhiệt ở qui trình hấp nhiệt, thời gian hấp nhiêt và thời gian dừng trong sóng hàn. Tốc độ tải điển hình được 4-6 ft / phút.
TẨM ƯỚT FLUX: (fluxer)
Máy tẩm ướt flux là một hệ thống để làm ướt bề mặt PCB bằng flux. Có ba loại hệ thống tẩm ướt được sử dụng, sủi bọt, sóng và phun. Fluxer phun là hệ thống ưu tiên cho công nghệ "không cần rửa" bởi vì nó cung cấp sự kiểm soát tốt nhất sự lắng đọng flux và sự bốc hơi bài tiết hoặc sự ô nhiễm khi flux chứa trong các thùng kín. Flux tham gia quá trình có nhiệm vụ để loại bỏ các oxit từ PCB và linh kiện để hàn và để thúc đẩy quá trình hàn.
Trong công nghệ "flux không cần rửa" (no-clean flux) tổng lượng của flux đưa vào bề mặt PCB là rất quan trọng để có được cách hàn tốt nhất và giảm thiểu dư lượng flux còn lại trên PCB. Hiện nay có hai loại flux "không cần rửa" được sử dụng, dựa trên gốc cồn và gốc nước. Bởi vì sức căng bề mặt thấp của flux gốc cồn nên dễ ướt hơn và dễ khô nên không nên hấp nóng thời gian dài và đồng thời không nên dùng sóng hàn kép. Flux gốc nước nói chung là mạnh hơn gốc cồn và yêu cầu hấp nhiệt đối cưỡng bức lưu mạnh mẽ hơn để sấy khô tốt. Bởi vì sức căng bề mặt của gốc nước cao nên bề mặt PCB không dễ ướt flux, trừ khi bề mặt đã được thêm vào hóa chất của nó.
HẤP NHIỆT:(preheat)
Mục đích của hấp nhiệt là để làm khô chất dẫn flux, thúc đẩy kích hoạt phản ứng hóa học mục đích làm sạch bề mặt hàn trên PCB và chân linh kiện, giảm sốc nhiệt cho PCB và các linh kiện để bắt đầu quá trình chuyển giao năng lượng nhiệt đến PCB chuẩn bị cho quá trình hàn. Bề mặt trên PCB điển hình có nhiệt độ khoảng giữa 180oF và 240o F.
HẤP NHIỆT BẰNG TIA HỒNG NGOẠI: (IR preheat)
Hệ thống sử dụng ống phát tia hồng ngoại như là nguồn năng lượng chính. Các ống được bao phủ với thủy tinh chịu nhiệt cao, nó trở thành một nguồn bức xạ thứ cấp. Phương pháp này cung cấp một bước sóng nhiệt trung bình được phát ra từ ống IR và bởi vì thủy tinh là có một nhiệt độ thấp hơn so với các ống, nên nó phát ra lại một bước sóng dài hơn. Phạm vi kết hợp là khoảng 5-7 micron. Điều này sẽ cung cấp một nhiệt độ thống nhất trên bảng mạch tốt hơn so với hấp nhiệt bằng chỉ có một nguồn chính. Tuy nhiên, có hai nhược điểm với hấp nhiệt hồng ngoại, đó là màu sắc chọn lọc nhiệt và không làm khô tốt với flux gốc nước. Như vậy màu tối hấp thụ năng lượng hồng ngoại tốt hơn so với màu sắc sáng hơn, nếu màu sắc của màu sơn phủ PCB thay đổi, lượng hấp thụ hồng ngoại sẽ thay đổi. Nước không hấp thụ nhiều năng lượng của IR và vì thế nước chủ yếu được làm nóng bởi bảng mạch. Điều này làm cho nó khó khăn hơn để bay hơi với flux gốc nước "không cần rửa" .
HẤP NHIỆT ĐỐI LƯU CƯỠNG BỨC: (forced convection preheat)
Trong hệ thống này, hệ thống sử dụng một tấm khuếch tán khí nóng cũng như làm nóng không khí khi nó đi qua các lỗ ở dạng tấm. Quạt gió lại lưu thông không khí nóng trở lại vào trong buồng và thông qua các tấm khuếch tán. Bảng mạch, linh kiện và flux hấp thụ năng lượng từ không khí nóng là như nhau, do đó PCB được làm nóng thống nhất. Từ đó đối lưu là một cách hiệu quả hơn để truyền năng lượng, khả năng của nó để làm khô flux gốc nước được tăng lên nhiều lần so với hấp nhiệt bằng hồng ngoại. Bởi vì đối lưu cưỡng bức không phụ thuộc màu nhạy cảm, thay đổi màu sắc sơn phủ sẽ có ít hoặc không có ảnh hưởng đến PCB
HÀN SÓNG: (solder waves)
Hàn sóng chính là trái tim của máy và là trung tâm của quá trình hàn. Các sóng hàn bao gồm sóng chính và sóng chip hoặc hỗn loạn. Sóng chính trong một quá trình hàn thường là một làn sóng tạo thành lớp với lưu lượng kiểm soát ở vòi phun. Trong một quá trình hàn N2 sóng chính là một làn sóng "A" được gọi là các coN2tour. Đây là quá trình dùng khí trơ trong khi hàn để gia tăng quá trình thấm hàn, giảm số lượng flux yêu cầu và mang lại mối hàn tốt đẹp sáng bóng.
Sóng chip hoặc sóng hỗn loạn thường được sử dụng khi có dán linh kiện mặt dưới PCB. Những biến động hỗn loạn của sóng chip giúp để phá vỡ các bong bóng khí sinh ra từ flux và đẩy các chất hàn lỏng đến xung quanh các góc chân linh kiện.
Chiều cao sóng là một tham số quan trọng vì nó ảnh hưởng đến thời gian dừng trong bể hàn và thoát khỏi bể hàn. Theo nguyên tắc chung độ cao sóng nên đến gần nửa độ dày của PCB, khi PCB vào các làn sóng hàn. Nhiệt độ của sóng thường được sắp xếp giữa 470o F và 500o F.
DAO KHÍ NÓNG: (hot airknife)
Đối với mạch mật độ cao và được sắp xếp theo các khối hình học chặt chẽ, hoặc khi qui trình có rất nhiều linh kiện, dao khí nóng được dùng như một tùy chọn để tách mối hàn bị bắt cầu, dao khí nóng là một phương pháp có bản quyền được đặt ở phía ra của bể hàn tạo ra một số lợi thế khác biệt.
CÁC LỢI ÍCH CỦA DAO KHÍ NÓNG: (Airknife Advantages)
Dao khí nóng thổi vào các mối hàn vẫn còn trong tình trạng nóng chảy khi bề mặt mạch hàn vừa ra khỏi sóng hàn. Các dòng phản lực của không khí nóng, hướng vào mặt dưới của PCB, phá vỡ sự dính hàn các mối nối bên ngoài, chạm trổ thêm lỗ hổng mối hàn, lấp đầy thiếc hàn khoảng trống bên trong mạ xuyên lỗ, gỡ bỏ các mối hàn ngắn mạch, loại bỏ mối hàn dư thừa thiếc hàn, cho thấy rõ nhiều vấn đề bám thiếc hàn và sửa chữa các mối hàn bị hư hỏng. Bằng cách gỡ các mối hàn bị nối trên PCB mật độ cao và có các khối hình học sắp xếp chặt chẽ, bạn có thể tăng năng suất bằng cách giảm số lượng việc sửa lỗi hỏng. Tỷ lệ khuyết tật thấp 2-20 PPM có thể đạt được trong các môi trường sản xuất lớn trên các hệ thống được trang bị với dao khí nóng để gỡ các mối hàn bị nối tắt.
Quan trọng không kém là kiểm tra. Mối hàn nối trông lành lặn và đáp ứng các tiêu chuẩn kiểm tra trực quan có thể bị che khuất khoảng trống trong một ống mạ xuyên lỗ, trường hợp này trong lĩnh vực lắp ráp dễ dẫn đến thất bại trước khi lắp ráp mạch hoàn chỉnh. Dao khí nóng "kiểm tra ứng suất" tất cả các mối hàn, với dòng phản lực không khí nóng trực tiếp ở mối hàn, ở một tỷ lệ 100 khớp mỗi giây hoặc nhanh hơn. Áp dụng với dòng phản lực không khí nóng ở khoảng 1.000 ergs/cm2(*) (lượng lực tác động xấp xỉ cần thiết để thổi bay phần dư thừa của mối hàn) sẽ không gây tác động xấu đến mối hàn lành lặn, hay mối dán keo linh kiện, nhưng sẽ phơi bày những mối hàn yếu có thể có lỗ hổng bên trong. Dao khí sẽ làm đầy chất hàn cho bên trong ống mạ xuyên lỗ mà cũng gây ra phát sinh khí trong mối hàn. Sự điền đầy này bị tạo bởi bọt khí xuất hiện bởi dao khí nóng và chất hàn vẫn nóng chảy thấm ngược trở lại vào lỗ mạ. Mối hàn đã đầy lại theo cách này sẽ xuất hiện như là một mạch chưa được hàn xung quanh chân của linh kiện. Tuy nhiên, sau khi kiểm tra chặt chẽ hơn, mối hàn sẽ được quan sát mức điền đầy các lỗ của linh kiện xuyên lỗ ở một mức độ nào đó. Tùy thuộc vào các tiêu chuẩn kiểm tra được áp dụng, nếu độ thấm chất hàn và lỗ hàn được quan sát thấy đạt, mối hàn là lành lặn thì coi như đạt yêu cầu
Một ưu điểm khác của dao khí nóng là rõ ràng nhận thấy hơn khi hàn SMD. Hệ số mở rộng cho các PCB chất nền thủy tinh /epoxy, các chân linh kiện, các mạch đồng và socket là khác nhau. Một lượng lớn của chất hàn trên chân linh kiện và mạch đồng sẽ gây ra ứng suất thừa cho mối hàn điều này dẫn đến khuyết tật mối hàn và gây hư hỏng sớm. Các dao khí nóng sẽ tinh sửa mối hàn , loại bỏ dư thừa hàn và làm cho các mối hàn dễ uốn hơn, và do đó giảm mõi cơ khí và lực căng do nhiệt.
ĐỘNG LỰC HỌC DAO KHÍ NÓNG: (Airknife Dynamics)
Dao khí nóng được tạo ra bằng tia hẹp (0.018"). Nhiệt độ dao khí nóng thường được điều chỉnh đến 750 ° F đến 850 ° F, và áp lực từ 4 đến 20 psi, tùy thuộc vào mật độ linh kiện, loại và hướng của PCB. Một trong các số thông số dao khí nóng có thể được điều chỉnh cho hiệu quả quá trình tối ưu là : góc hợp theo phương ngang từ 40 đến 90 ° và khoảng cách càng gần càng tốt mặt dưới của PCB. Nếu quan sát mối hàn từ phía trên PCB thấy có bắn tung tóe chất hàn, thì phải chỉnh nhỏ áp suất khí nóng của dao xuống dưới 1 PSI rồi chỉnh dần lên cho đến khi hết nối cầu mối hàn so với khi không có thổi. Một đề nghị với áp suất khí thổi từ 5-10 PSI, nhiệt độ 800oF (426oC) và góc 65o cho một kết quả tốt nhất với tất cả loại lắp ráp PCB
(*) erg là một đơn vị đo năng lượng và làm việc cơ khí trong một centimet gam giây (CGS). Ký hiệu là: erg. Tên nó có nguồn gốc từ từ "ergon" của tiếng Hy lạp có nghĩa là "làm việc"
Một erg là lượng làm việc được thực hiện bởi 1 lực bằng 1 dyne tác dụng trên khoảng cách là 1 cm. Đơn vị cơ sở CGS là gam centimet trên giây bình phương (g.cm2/s2).
Vì thế nó bằng 10-7 (J) hay 100 (nano J) trong hệ SI
1 erg = 10-7 J hay 100 nJ
1erg = 624.15 GeV = 6.2415 x 1011 eV
1erg = 1 dyne cm = 1 g.cm2/s2
Viết bình luận